Listen to this article
|
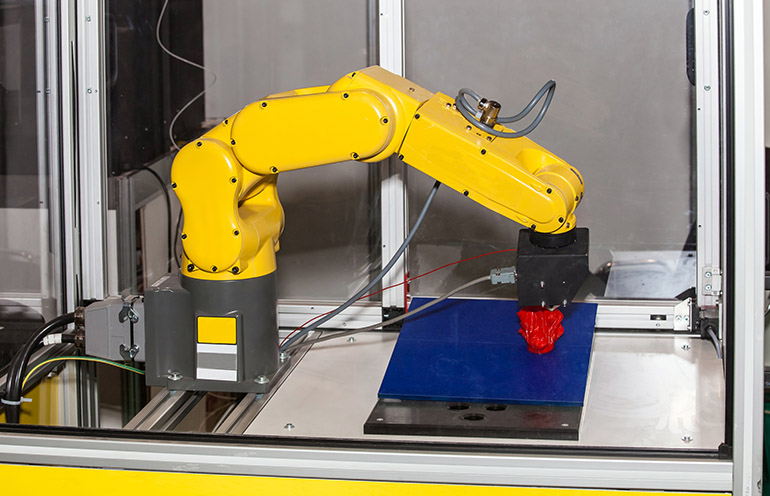
Robotic arms in large-scale 3D printing deposit materials layer by layer, transforming production. Source: Replique
In the realm of modern manufacturing and automation, the integration of robotics continues to redefine industry standards. One technology that is pushing the boundaries of what’s possible is 3D printing. Henrike Wonneberger, co-founder and chief operating officer at Replique, explores the relationship between additive manufacturing and robotics.
Here, she highlights the technology’s impact and potential for enabling flexible, customized, and lightweight production within the automation industry.
Additive manufacturing can unlock customization
Central to the evolution of robotics is the ability to create customized components efficiently. Traditional manufacturing methods often struggle with the cost and complexity of producing bespoke parts like grippers and intricate assemblies.
Additive manufacturing enables manufacturers from small and midsize enterprises (SMEs) to large corporations to produce customized parts on-demand. With it, they can do so without the constraints of tooling or minimum order quantities.
This flexibility is enabled by the digital nature of the technology. Unlike traditional production methods such as injection molding or casting that require a lot of time and effort to set up, 3D printing allows for immediate production, as it seamlessly translates digital designs into physical objects by layering materials.
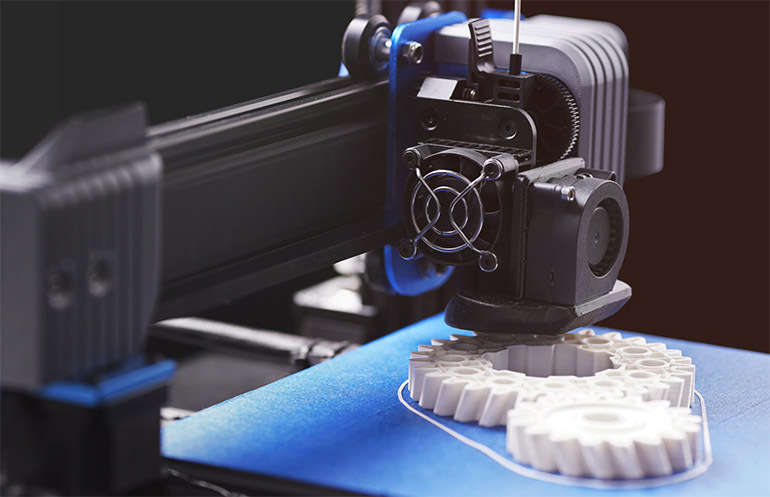
Additive manufacturing plus robotics can transform industries. Source: Replique
Optimize performance with lightweighting
Another key advantage of 3D printing in robotics lies in its capacity to optimize weight and enhance performance through innovative design. By allowing engineers to create complex geometries and hollow structures, additive manufacturing can reduce material waste and improve structural integrity.
Lighter parts can also extend the operating life of robots by reducing wear and tear on the system, thus reducing maintenance intervals. For instance, optimized grippers can further contribute to faster speed on the production line.
Lastly, thanks to lightweight construction, smaller and lighter robots can be created for heavy-duty applications. In the medium term, this approach reduces energy consumption and lowers CO2 emissions, underscoring how such production can enhance both performance and sustainability in robotics.
Humanoid robots, with their need for safety and to squeeze as much power out of batteries as possible, represent an extreme and emerging case for lightweighting.
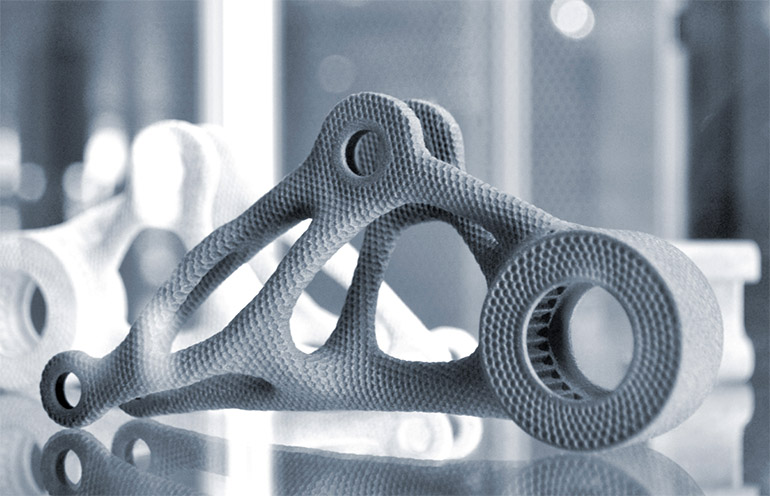
Additive manufacturing enables the design and production of lightweight parts. Source: Replique
3D printing helps streamline assembly, enhance flexibility
Beyond customization, 3D printing can simplify assembly processes by consolidating multiple parts into single, integrated components. This approach not only reduces assembly time and inventory complexity, but it can also minimize potential points of failure and improve overall reliability.
Industries across sectors, including automotive, aerospace, and the food, can benefit from parts consolidation. In food processing, for example, additive manufacturing can reduce the number of robot joints and connection points, enhancing hygiene by minimizing places where bacteria could accumulate.
On the other hand, it also allows for dividing one part into different components, facilitating easier changes of format parts as needed.
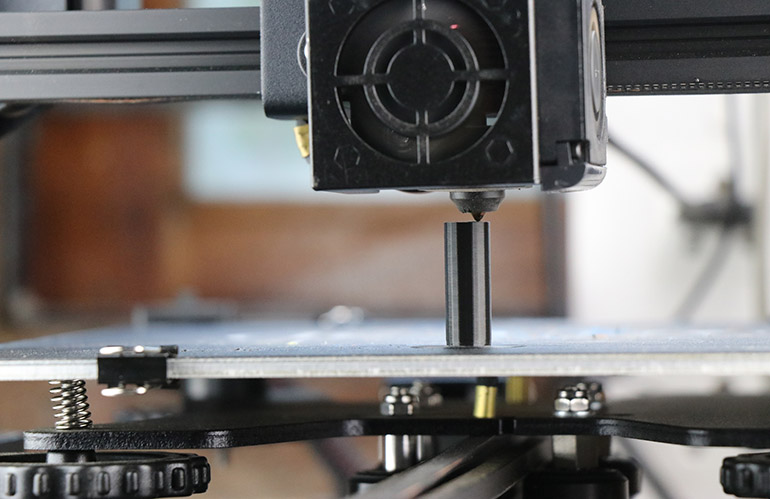
3D printing empowers small players to create cost-effective robot parts with no minimum order quantity, starting from lot size. Source: Replique.
Robotics can benefits from agile prototyping and iterative design
The iterative nature of 3D printing accelerates the prototyping and design validation process in robotics.
Engineers can rapidly translate conceptual designs into functional prototypes, facilitating quicker design adaptions and reducing time-to-market. This enables continuous improvement and adaptation to evolving technological requirements in the robotics and automation industry.
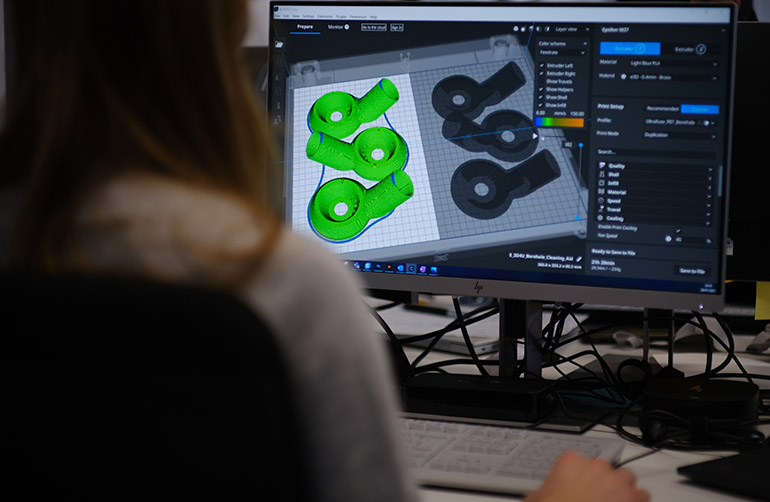
Additive manufacturing allows for fast iterative design. Source: Replique
Get spare parts on demand for operational resilience
In operational environments where downtime is costly, the ability to produce spare parts on demand is invaluable.
3D printing enables rapid, localized production of replacement components, significantly reducing lead times and inventory costs. This capability ensures continuous operational readiness of robotic systems, enhancing overall efficiency and minimizing disruption.
3D printing: From grippers, soft robotics to integrated systems
Format parts, such as grippers, are ideal use cases for additive manufacturing. It allows manufacturers to create these components with high customization, reduced weight and cost. Format parts can be easily optimized and changed for specific application.
For instance, a Replique collaboration with struktur.form.design Engineering GmbH, reduced the weight of a collaborative robot gripper by 78%, part count by 84%, and production costs by 30% through redesign and additive manufacturing.
Beyond that, additive manufacturing supports innovations in soft robotics, enabling the creation of flexible, adaptive structures for precise movements, e.g. in the medical prosthetics industry.
In addition, integrating sensors and electronics directly into 3D-printed components can enhance functionality and streamline assembly processes.
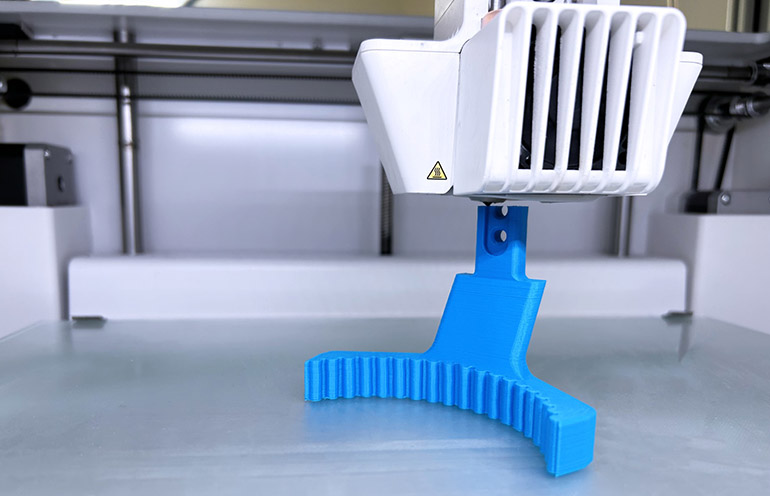
A soft gripper is one example of how additive manufacturing enables robotics. Source: Replique
Robots as 3D printers themselves
The synergy between robotics and 3D printing can extend beyond traditional applications. Robots themselves can act as 3D printers, expanding the scope of additive manufacturing.
In large-scale 3D printing, robotic arms can deposit materials layer by layer to create objects, enabling the production of parts on a scale previously not possible in 3D printing. This has shown promise in metalwork and construction.
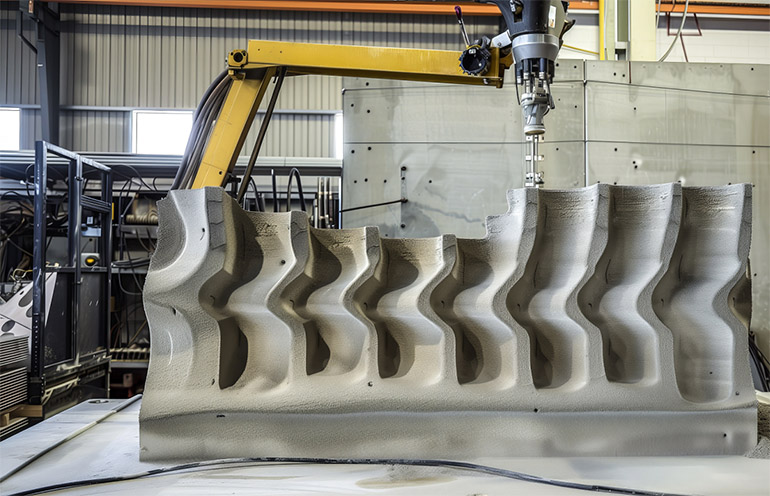
Robots can be a part of 3D printers themselves. Source: Replique
Pioneer the future of robotics with 3D printing
The integration of additive manufacturing technology into robotics represents a paradigm shift in manufacturing capabilities.
From customized components to enhanced operational resilience, 3D printing enables more agility, innovation, and efficiency in the robotics and automation industry.
About the author
Henrike Wonneberger is the co-founder and chief operating officer at Replique GmbH. The Mannheim, Germany-based spinout of the BASF Digital Transformation Initiative provides an industrial 3D printing platform to enable companies to deliver on-demand parts globally through a decentralized and secure network.
Tell Us What You Think!